The Science Behind Porosity: A Comprehensive Guide for Welders and Fabricators
Recognizing the detailed systems behind porosity in welding is vital for welders and producers striving for impressive craftsmanship. From the structure of the base materials to the details of the welding procedure itself, a wide range of variables conspire to either exacerbate or relieve the presence of porosity.
Understanding Porosity in Welding
FIRST SENTENCE:
Assessment of porosity in welding reveals critical insights right into the stability and high quality of the weld joint. Porosity, identified by the presence of dental caries or voids within the weld steel, is an usual issue in welding procedures. These voids, otherwise properly dealt with, can endanger the structural stability and mechanical properties of the weld, bring about potential failures in the completed item.
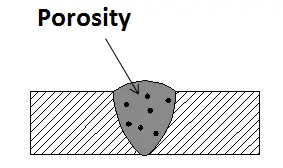
To discover and measure porosity, non-destructive screening approaches such as ultrasonic screening or X-ray inspection are typically utilized. These methods permit the recognition of inner defects without compromising the integrity of the weld. By evaluating the size, shape, and distribution of porosity within a weld, welders can make educated decisions to enhance their welding processes and accomplish sounder weld joints.
Factors Influencing Porosity Formation
The incident of porosity in welding is affected by a myriad of aspects, ranging from gas securing efficiency to the details of welding specification setups. Welding specifications, consisting of voltage, present, take a trip rate, and electrode type, additionally effect porosity formation. The welding strategy utilized, such as gas metal arc welding (GMAW) or protected steel arc welding (SMAW), can affect porosity formation due to variations in heat circulation and gas coverage - What is Porosity.
Results of Porosity on Weld High Quality
The existence of porosity likewise compromises the weld's resistance to rust, as the trapped air or gases within the voids can respond with the surrounding setting, leading to deterioration over time. Furthermore, porosity can impede the weld's ability to withstand stress or influence, additional jeopardizing the overall top quality and integrity of the welded structure. In critical applications such as aerospace, auto, or architectural buildings, where safety and durability are extremely important, the damaging effects of porosity on weld top quality can have severe effects, highlighting the significance of minimizing porosity via appropriate welding techniques and procedures.
Techniques to Decrease Porosity
To boost the high quality of bonded joints and make sure structural stability, welders and fabricators use details methods aimed at minimizing the formation of spaces and cavities within the product during the welding procedure. One efficient method to lessen porosity is to guarantee correct material preparation. This consists of thorough cleaning of the base steel to eliminate any kind of pollutants such as oil, oil, or moisture that might add to porosity development. Additionally, utilizing the ideal welding parameters, such as the proper voltage, current, click reference and travel rate, is important in avoiding porosity. Maintaining a constant arc length and angle throughout welding additionally helps minimize the likelihood of porosity.

Furthermore, selecting the ideal shielding gas and keeping correct gas circulation prices are important in reducing porosity. Utilizing the appropriate welding technique, such as back-stepping or utilizing a weaving movement, can likewise assist distribute warmth equally and lower the opportunities of porosity development. Guaranteeing appropriate ventilation in the welding atmosphere to eliminate any potential resources of contamination is essential for attaining original site porosity-free welds. By carrying out these methods, welders can properly decrease porosity and create premium welded site link joints.
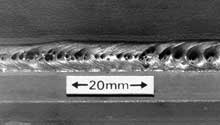
Advanced Solutions for Porosity Control
Applying advanced modern technologies and innovative techniques plays a critical duty in achieving remarkable control over porosity in welding processes. Furthermore, using advanced welding methods such as pulsed MIG welding or changed environment welding can also assist minimize porosity issues.
One more sophisticated remedy involves using advanced welding devices. For example, making use of equipment with built-in functions like waveform control and innovative power resources can enhance weld top quality and reduce porosity dangers. Additionally, the application of automated welding systems with exact control over criteria can dramatically minimize porosity problems.
Additionally, integrating advanced monitoring and examination modern technologies such as real-time X-ray imaging or automated ultrasonic screening can assist in identifying porosity early in the welding procedure, permitting prompt rehabilitative activities. Generally, incorporating these sophisticated services can significantly improve porosity control and enhance the total top quality of welded elements.
Final Thought
In final thought, understanding the scientific research behind porosity in welding is vital for welders and fabricators to generate top notch welds - What is Porosity. Advanced services for porosity control can better enhance the welding procedure and ensure a solid and dependable weld.